As a member of the EEBA community, you play a crucial role in leading the way towards constructing homes that are high-performing, healthy, and resilient.
Now aligned with this objective are the self-educated homeowners and prospective buyers who are demanding high-performance homes. Because of this, builders (as well as the raters and architects who support them) are looking for product solutions that:
- Add value to their customers’ investments
- Demonstrate a core commitment to being a “responsible” builder
- Differentiate themselves in a competitive marketplace
Our hope at Stego (and the purpose of this article) is to help provide useful support and education so that EEBA builders can better understand vapor transmission at the first side of the home - the foundation - and the role below-slab vapor barriers play in achieving high-performance goals in new homes.
No, we are not talking about commodity 6 or 10-mil poly sheeting. Minimum residential code (2021 IRC Section R506.2.3) no longer allows generic poly sheeting beneath concrete floor slabs as a vapor retarder. Evaluating and selecting vapor barriers (or “retarders”), beneath a concrete slab, necessitates different considerations and product performance benchmarks compared to how we think of controlling vapor across the building enclosure (like in the walls).
Quick Note: although this article focuses on vapor protection beneath concrete slabs (on-grade or in a basement), much of the science, material performance considerations, and goals apply directly to crawl space construction as well. In many ways, effectively controlling vapor from the ground in a crawl space (any crawl space, but especially unvented, conditioned crawl spaces) is even more critical to the performance, durability, and indoor air quality of the home. You can learn much more about crawl space vapor protection at www.stegoindustries.com/blog
Basic Building Science: Water Vapor Movement Into the Home Through the Slab
Regardless of where a home is constructed, there is moisture in the ground at some depth below (generally the water table) or around the foundation -- think of rain falling to the ground and seeping into the soil, for example. We go to great lengths to prevent the infiltration of bulk liquid water into the home’s foundation through proper drainage, capillary breaks, waterproofing, etc.
However, water vapor – the invisible/gaseous form of water – is also continually “working” to move into the interior of your home.
The basic building science principle, in simplified form, is that water vapor moves from “more to less.” In the below-slab environment (the ground beneath the home) water vapor is 1) always present and 2) abundant, compared to the interior of your home.
This movement of water vapor from higher to lower concentrations is known as diffusion and is one of two primary means by which water vapor will migrate through the foundation of a home.
The second way water vapor can move into the home from below is advection. Advection is the process where vapor is carried in a medium (in this case, air) due to pressure differentials. This bulk air, as well as the water vapor or soil gases (more on this later) within it, will find pathways to enter, the often lower-pressure, interior environment of the home – through any holes, leaks, or other discontinuities in the building enclosure.
We can shut down advection by creating an air-tight enclosure, but as long as there’s a water source beneath the home (and there always is), diffusion never stops.
What makes matters worse for your home’s foundation is that concrete – despite it being hard and durable – is not vapor-proof. Left unchecked, water vapor will continually diffuse toward the interior of the home and through the concrete slab-on-grade or basement floor over time.
Concrete will slow water vapor down, but other components in your slab assembly, like flooring, can stop it – many flooring or adhesive materials is like having a “vapor barrier” on the wrong side of your assembly. This is where long-term problems can occur: water vapor can accumulate and develop a higher localized relative humidity in the concrete slab. When it can’t hold any more vapor and a surface below the dew point temperature is present (such as beneath the flooring system within the cooler, conditioned home), condensation can occur, a common culprit for moisture-related flooring failures, mold growth, or other issues. Thus, stopping this natural movement of water vapor beneath the slab is absolutely critical.
Protect the Home with Below-Slab Vapor Protection
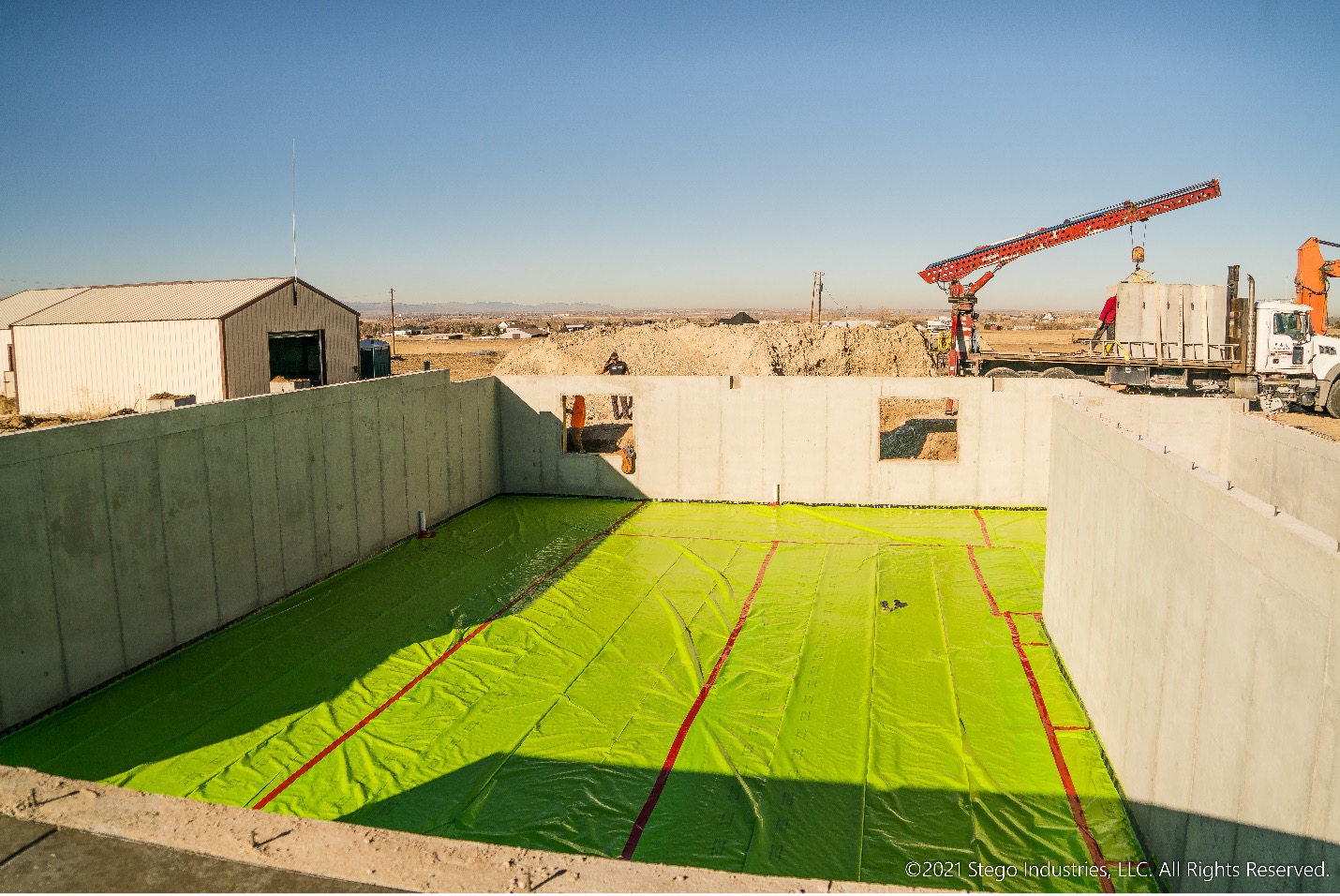
A below-slab vapor barrier or vapor retarder, a thin-gauge plastic sheet, is typically installed directly beneath concrete floor slabs. But, while it may strike some as “a sheet of plastic,” the below-slab vapor barrier is not simply a commodity, but an important component to the home’s enclosure and its overall long-term performance.
The Role of Foundation Vapor Control in a High-Performance Home
Generally, our collective goals in achieving a high-performance home include maximizing human health, durability, and energy performance, as well as reducing environmental impact.
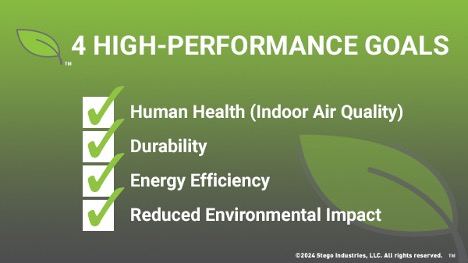
Let’s look a little closer at these four high-performance goals and how effective below-slab vapor protection fits in.
1. Human Health (Indoor Air Quality): although there are many components to a healthier home, a critical piece is reducing the presence of harmful indoor air pollutants and contaminants to improve indoor air quality (IAQ). Ventilation and filtration are a big part of the equation, but it starts with controlling unwanted contaminants from entering or developing.
Mold has been a hot-button topic for decades because its growth in homes has the potential to cause health problems for occupants. However, mold can only survive in an environment with sufficient moisture. Making sure the home stays dry and at an appropriate interior relative humidity will help prevent the potential for harmful mold growth. Effective below-slab vapor barriers help take the ground moisture out of play.
Another common health concern for new homes is radon gas. Radon is a naturally occurring gas in soils that, like water vapor, can move into the home from beneath the foundation as we described earlier. Radon is the second leading cause of lung cancer in the United States and most new homes (and many older ones), now incorporate radon mitigation systems. A below-slab vapor barrier (also referred to as a “soil-gas retarder” when serving in the mitigation system) is an important component for radon-resistant new construction.
2. Durability: there is a tremendous impact on a home’s performance when parts aren’t built to last or simply need avoidable maintenance over time. Replacing or fixing building components generates waste and can have an impact on both the time and wallet (and probably sanity) of homeowners. More and more homebuilders understand they need to bring their potential customers genuine quality and value from the start.
The transmission of moisture vapor into a home from below the foundation can have a negative impact on building components. Most common and costly among these impacts is the potential for floor covering and adhesive failures.
Whether it is a basement or slab-on-grade, you only have one good chance to put effective vapor protection beneath your concrete floor. Once your concrete slab is placed, there is no easy do-over. Doing it right the first time is critical not only for homeowner peace of mind but potential liability for builders. An effective and properly installed below-slab vapor barrier can represent a maintenance-free, permanent solution.
3. Energy Efficiency: energy performance is often a top priority when endeavoring for high-performance homes. It’s critical to the comfort, operational costs, and overall embodied environmental impact of a home. There are, of course, many ways to design and construct a more energy-efficient home.
But one factor in energy efficiency is also creating tight, well-insulated homes that reduce the load on the HVAC system. Again, not simply airtight, but also effectively controlling water vapor that can potentially increase humidity in the home.
Passive solutions to maintaining a comfortable temperature (reducing air leakage, utilizing insulation) and preventing the ingress of unchecked water vapor—which adds to the latent load and can adversely affect building materials—can be a contributor to improved energy efficiency.
4. Reduced Environmental Impact: high-performance homes often also make an obvious connection to goals around environmental responsibility. For example, more durable homes mean fewer repairs and replacement of components, meaning less waste to the landfill and reduced carbon emissions associated with that work. But we can also look holistically at the building products themselves and their impact on our future world.
There has been a lot of progress in the building product landscape with how products are engineered, understanding greenhouse gas emissions along the product lifecycle, and manufacturer commitments around environmental and social health. Homeowners and builders can make better-informed choices about products with transparent information available that helps explain things like ingredients, volatile organic compound (VOC) emissions, and potential human health hazards of building products, as well as the embodied carbon and corporate responsibility of the companies who make them.
So, what should homebuilders, raters, and architects look for when incorporating a below-slab vapor barrier into a new home?
-
Low Water Vapor Permeance: look for a vapor barrier that provides a very low water vapor permeance rating, which is the measure of how easily water vapor moves through the material. In this application, the lower the permeance, the better. A “vapor barrier” permeance of 0.01 perms or less is an industry-established threshold for below-slab applications and will significantly reduce the amount of potential water vapor that can contribute to moisture-related concerns in the home. Compare that to generic, 6-mil polyethylene sheeting, and a vapor barrier with less than 0.01 perms can provide upwards of a 90% reduction in yearly water vapor transmission through a 1,300ft² new home footprint.
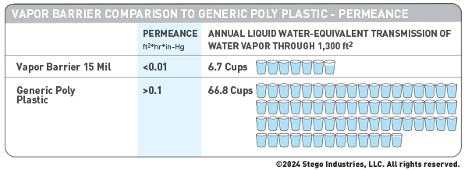
- Meets ASTM E1745: this is a published industry performance standard and outlines minimum requirements around strength and permeance, but also includes conditioning testing which simulates the below-slab environment. Products that meet this standard are engineered to withstand the rigors of construction and resist long-term deterioration beneath the slab. Generic, off-the-shelf polyethylene sheeting (often 6-mil thick) does not meet this performance standard and can present critical problems beneath a concrete slab. In fact, the 2021 IRC now requires vapor retarders beneath concrete floor slabs to meet ASTM E1745), as well as be a minimum 10-mil thick.
- Effective Installation: like any building enclosure component of a new home, proper installation and detailing are often critical to the performance of the system. For the below-slab vapor barrier, an effective installation is not only useful for preventing water vapor diffusion, but also to help create an air-tight system to impede the bulk movement of soil gases like radon or moist air due to pressure differentials. Look for a below-slab vapor barrier that has a full, integrated system approach to the installation, as well as the details and support to ensure it is done effectively and efficiently. Get a 5-Step Guide to Installing a Residential Below-Slab Vapor Barrier.
- Prioritize Peace of Mind and Support: consider the manufacturer behind the vapor barrier product. This is where you begin to see significant differences in product quality and consistency, warranties, sales and marketing support, installation training for trades, and commitments around environmental and social responsibility. For many homebuilders, raters, and architects (as well as the future homeowners), these things go hand-in-hand with the performance, availability, and costs of products and align with the overall goal of a better home.
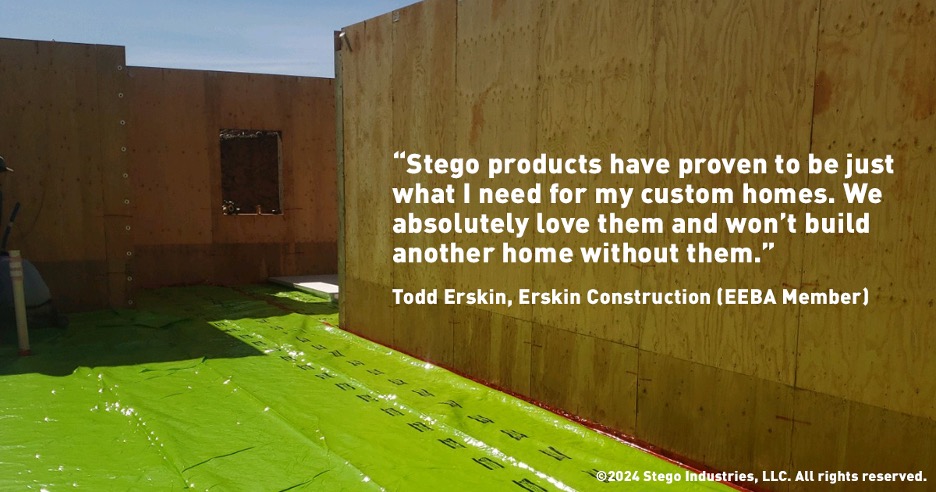
High-Performance, Healthy Homes Start from the Ground Up
Still think it’s “just a sheet of plastic?” A lot of engineering, chemistry, and building science goes into this integral product for the home’s foundation! More importantly, for EEBA builders focusing on high-performance homes, the inclusion of superior below-slab vapor barriers is an economic decision that should not be overlooked. Its upfront cost is relatively minor in the grand scheme of building expenses, yet it plays a significant role in the long-term performance and sustainability of homes.
Stego is here to equip EEBA builders with the confidence to navigate the nuances of foundation vapor protection with industry-leading barrier solutions. Contact us to learn more about our solutions – including StegoHome® Below-Slab Vapor Protection – and lean on industry-leading support every step of the way to tackle your next build.
View original blog on Stego’s website
Discover the Benefits of StegoHome®
Visit Stego’s Blog to learn more!