Installation of the air barrier and then testing of that air barrier are the most challenging parts of the residential energy code and have been since 2012. It's not something that you can get by with ignoring and hope you're going to pass. It is a challenge. It is essential to pay attention to these details if you don't want to have a problem with compliance at the end of your build.
With air sealing, we're trying to control air movement and, consequently, convective heat movement and heat loss, whether from the inside outs or the outside in. Air sealing is also essential for helping to control moisture movement in humid environments. Some of the tools that you'll see people use to control air movement include caulks, sealants, rigid exterior insulation, certain spray foams, and continuous rigid board.
Code air barrier requirements have changed significantly since 2009 when they were just an alternative to conducting a blower door test. For those unfamiliar with a blower door test, it is essentially a process that depressurizes a building and then measures the amount of air leaking through the building envelope. The results are usually expressed in air changes per hour (ACH) at a specific pressure. The code stipulates that we test at a pressure level of 50 pascals, and we measure how many times the air will change in a space within an hour at that high depressurized level. We pump a lot of air in or out of a house and measure how much air is leaking through the cracks and the holes in the building's envelope. That's how it works.
In 2009, the code allowed for up to seven ACH, which was easy to achieve even at the time, but nobody had to do it if you could pass a visual air barrier inspection after sealing all the items on the air barrier installation table, a detailed checklist. In 2012 that changed in a big way.
First, it required compliance with the air barrier installation table and follow-up visual inspection while adding a mandatory blower door test. For climate zones three to eight, the air barrier was three air changes per hour at 50 pascals. For climate zones one and two in the very southern portion of the country, it allowed up to a five ACH at 50 pascals. Again, I know many builders who are going well beyond that now but, for somebody first having to meet this airtightness target, that was new, and many jurisdictions around the country amended that requirement when they adopted the 2012 code. In the 2015 and 2018 IECC, we have those exact requirements. If you missed the mark and the house doesn't pass either test, you wouldn’t get your Certificate of Occupancy. It wasn’t something where you could find efficiencies somewhere else and refile the plans under performance paths and pass anyway. A failure is costly.
Now, in 2021, we have slight changes. While the air barrier inspection and blower door test are still mandatory, there is some flexibility for climate zones three through eight. Suppose you’re doing the prescriptive compliance option. In that case, you must meet that three ACH 50 but, if you use one of the performance paths, section four, or five or 406, you have flexibility up to five ACH 50 if you can still meet the overall energy performance targets for those compliance paths. I don't know how often that will be used because both of those paths are challenging in their ways. (There were already five ACH 50 in climate zones one and two, so there's no added flexibility for those climate zones.)
Another option that's been added in the 2021 code is compartmentalization tests. One of the challenges of a volume-based air leakage test is that smaller units tend to have a more challenging time passing because the same amount of leakage in a smaller unit is a more significant piece of the pie. So that's harder.
Also, attached products (like multi-unit dwellings) historically have issues caused by air sealing the common walls between units. The code now offers two different ways of measuring air leakage. In some circumstances, any dwelling, even a single-family home, can now be a .3 CFM (cubic feet per minute) per square foot of dwelling unit enclosure area. That means CFM at 50 Pascal's. It’s the leakage measurement by the home’s surface area, so the ceiling, the wall, the floor, all the different nooks in the house will define your surface area. It's measured by the surface area as opposed to value measurement. Historically, it is how multifamily buildings were measured for air leakage before the code requirement came into effect.
Also, .28 CFM can be used in any dwelling. The higher allowance of .3 CFM is for attached homes, or multifamily units that are three stories or less, or a small building allowance for under 1500 square feet. So that may help; in some cases, it’s very dependent on geometry and size and tends to be a slightly easier target to hit than the ACH 50 number.
This is just another option. If you don't want to do the five ACH or the three ACH or five ACH 50 tests, you can do .2, eight CFM 50 for any dwelling, .3 for attached dwellings, multifamily, and small units. If you've got somebody testing the house, and it doesn't pass the volume, you can look at this as a different way of measuring to see if the house can comply.
Regardless of the target, you need to know where your air barrier is if you're going to pass. If you don't, you’re not going to pass your blower door test, except possibly by luck. The details must be on the plans. If your air barrier is building paper on the exterior, then that needs to be detailed, and there are specific details that must happen with that building paper. If your air barrier uses drywall on the interior, your air sealing details will look slightly different. If you can't track where that air barrier goes, you're going to miss something. It's an essential part of planning out a house that's got to comply with the IECC.
Now I will talk about specific details that the code calls out in the air barrier installation table. All these details are mandatory. In the 2021 code, they don't use the term mandatory; but they’re required in all three set code compliance paths. Everything I read now must be done, and if it's not done, that's enough to fail the house until it's fixed. All these things are meant to get you closer to meeting that blower door test number.
One of the main requirements is that the air and thermal barriers must be installed in continuous alignment. When they're not continuously aligned, we tend to have issues where the air moves, making especially air-permeable insulation ineffective.
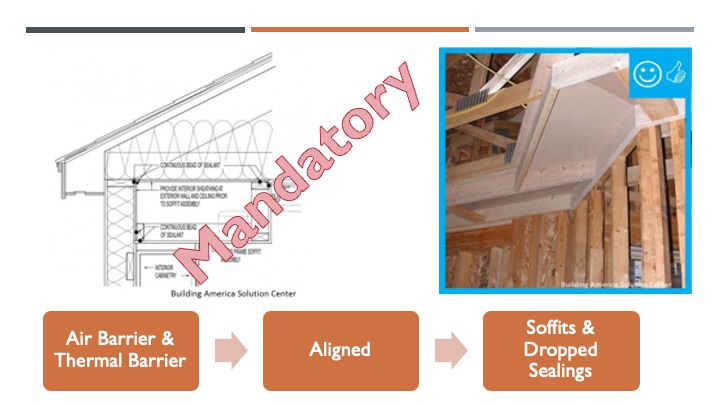
With any dropped soffits and ceilings, the air barrier must be aligned with the insulation. So, you see on the left here, beads of sealant marked on the plans are aligned with the insulation, not with the bottom of the soffit where the thermal barrier doesn't exist. That's a mandatory detail in the code.
Access hatches and doors must be air-sealed. This could be done with a gasket or other type of weather stripping. If we're using continuous insulation as part of the air barrier, so the insulation is creating part of the air barrier, taping all the joints and seams is also a requirement.
The top plate is where we see many leakages, so the code says you must air seal it. Now, it could be that that joint is sealed in several different ways. It could be an aerosolized seal and caulked or part of a liquid-applied air barrier on the exterior; there are many ways to seal these joints that are not necessarily caulking between them, but that is also a possibility. This is a mandatory detail in the code.\
The foundation and sill plate joint must be sealed because it is an area of typical air leakage and the cause for a lot of failed blower door tests. This area is particularly problematic because you have a straight piece of lumber sitting on a foundation that may have bumps and curves, so there are many places for air infiltration. You can seal this area with gaskets, foams, caulks; any are allowed but, you must seal that joint.
One of the additions in the 2021 code is that basements, slabs, and unvented crawlspaces must be sealed anywhere there's a penetration in the foundation or slab. The code already requires that we seal any penetrations. Still, these penetrations are specifically called out if anybody had a question about whether to seal a pipe running through the slab or something like that. The code says yes. You do have to air seal it.
Any joints from knee walls going from conditioned to unconditioned space must be sealed. Window and door jams must be sealed, and they cannot use air-permeable insulation like fiberglass. Almost every window installer who's ever come to my house has tried to do this. They go round and cut all these tiny strips of fiberglass and stuff them around the windows. First, it's not insulating anything because fiberglass loses its insulating properties when you compress it. And fiberglass is an air-permeable insulation, which means the air will move through it. It’s also not stopping any air leaks. Those are considered unsealed joints, and they need to be sealed according to code; otherwise, it’s enough to fail a house.
If you have a space that’s less than one inch, the code now says you can air seal it instead of insulating it. And that makes much sense because there's not a lot of insulating products, other than spray foam or something like that, that's going to be able to get into a space that size, air seal, and insulate it.
Rim joists must be sealed. They must be insulated. They also must include an air barrier. You cannot skip the air barrier in the rim joist, even on a floor over unconditioned space. The code says all rim joists must be part of the air barrier, even if you're not insulating the basement below. 2021 adds some new details to the rim joists requirement to include the exterior air barrier, the rim board, and the sill plate junction -- all must be sealed to the subfloor. This is how you would seal it anyway but, the 2021 code provides specific details for that assembly.
An air barrier must be installed at the exposed edge of any floor insulation. That means that we can't have unexposed floor insulation in a floor over an unconditioned space. If you've got an exposed edge of insulation at the floor, the air barrier must be installed at that location.
Anywhere where you've got a duct shaft or penetration of any kind for utilities, for example, for flues or pipes, it must be sealed in a manner that allows for expansion and contraction. The code doesn't give much more detail than that, so it's a little vague on what's specifically required but, the concept is that you shouldn’t use a ceiling material that won’t allow for expansion and contraction when you've got materials that have hot and cold air going through them.
As for lighting, if the recessed lighting penetrates the thermal envelopes, like when top floor lighting goes into the attic, you must seal the fixtures. The insulation section also requires that the unit be IC-rated if it’s going to meet the insulation. So, to summarize, the fixture itself is sealed and, the light itself must be sealed to the finished surface. Both these steps are mandatory.
Air barriers are required behind tubs and showers on exterior walls to avoid air movement behind that space. The same applies to electrical boxes. The code says that if you don't have an external air barrier behind electrical boxes, all the boxes must be sealed; otherwise, there could be a significant amount of air coming in through the holes in the electrical boxes. Pre-gasket boxes and kits are available, or you can install the air barrier behind all the electrical boxes.
Anywhere where you have a duct register boot penetrating the thermal envelope, you must have that sealed to the subfloor. This will affect both your duct blaster test and your blower door test. Often, when this doesn’t happen, it ends up being a scope-of-work issue. The HVAC contractor says, well, that's the carpenter’s job, and the carpenter says, it's the painter’s job, and the painter didn't think anything except painting was their job. In that sort of a situation, clearly defining who's responsible for what air sealing step can help avoid this common problem.
The IRC has required fire sprinklers since 2009, but they're not adopted in many states. The problem is that for specific kinds of fire sprinklers, you can't traditionally seal them because it will prevent them from moving, which they need to do to function correctly. This doesn’t tend to be a problem for pendant heads because you can seal the joint at the finished surface. But concealed sprinkler heads drop down to function but, the code says they must be sealed. The good news is that most fire sprinkler manufacturers have specific products designed for air sealing code requirements. If you need to install a concealed head, look for the product that is made to be sealed because otherwise, not sealing them may be the difference between passing or failing that blower door test.
Fireplaces must have tight-fitting doors or dampers, and if they are a factory-built model, as many of these fireplaces are now, they will have to meet a specific UL listing. You can still have a wood-burning fireplace in a home that's built a three ach 50, but it takes some careful design because it won’t draft the same way it did in that seven ACH or 10 Ach 50 house.
Now, for anyone who builds townhouses or other attached products in a state that's adopted the IECC and has this three ach 50 Target, you'll know that this is a challenging target to meet for townhouses. Getting to three ach 50 with common walls between units is a challenge. Part of the reason is that it tends to be a leaky part of the assembly. Another factor is that there's not much clarity in how you air seal these without violating the fire-rated assembly. Firewalls have specific attributes, including air gaps that are part of the assembly. If that air gap gets filled with sealants or foams to stop the air leakage, it can act as a fire fuel source. Likewise, if you cover the breakaway clip, it's unclear how the breakaway clip will behave. If you caulk instead of foam, is that better? There have been many questions, and in the jurisdictions that adopted the air sealing requirements early, townhouse builders have been scrambling for several years to find answers. Several groups are working to solve this issue. There have been some breakthroughs recently with retesting fire-rated wall assemblies with specific foams and sealants to show that they will perform, and several options are now listed in the UL database. (Watch the webinar for the complete discussion.)
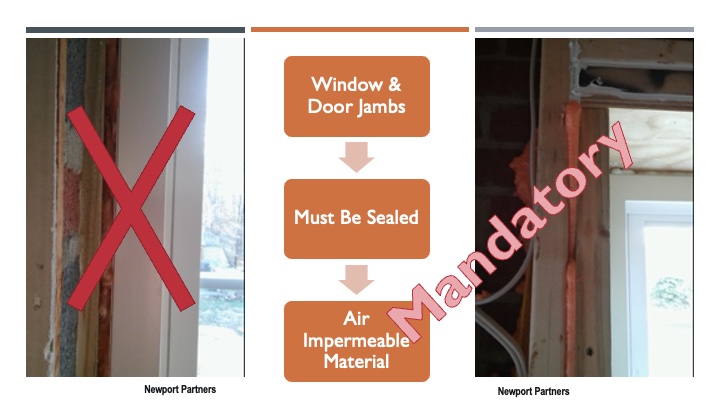
All windows installed per the IECC must have .3or lower air leakage. You need to make sure that your windows, if they're going in somewhere, that's adopted the IECC, got to have that air leakage test on it, and it's got to be lower than .
One of the things I always get asked is, “aren't we building houses too tight?” And “why don't we make the houses looser so they can breathe?” And the answer is that we can't. To get enough fresh air for us to breathe, we would need to build homes around a 14 ACH 50, and I don't know if anybody has built a 14 ACH 50 in the last 30 years. Even houses that fail the blower door tests aren't failing at 14 ACH 50 for new construction. We're building it tight and saving energy by doing so, and we must ventilate. It’s the only option. And no, opening windows isn't a trade-off against mechanical ventilation. It has never been. I'm certainly not going to open my windows this week when it's 12 degrees outside or when it's 100 degrees and 90% humidity outside, are you? We must ventilate to get fresh air. It's the only responsible way to build.
Joe Nebbia - Research Associate, Newport Partners
Joe Nebbia is a building codes expert with 15 years of experience in policy and regulatory analysis, including over a decade spent working on buildings and construction-related issues. He participates in multiple codes and standards developing processes, including the International Code Council, ASHRAE, and state codes.
In addition to code development and advocacy, Mr. Nebbia teaches code classes to builders, designers, code officials, and others in multiple states. Daily, Mr. Nebbia answers industry and government official technical questions regarding the International Energy Conservation Code. Mr. Nebbia has led various economic and market research efforts, authored various housing economics reports, and developed multiple industry roadmaps. A trained meeting facilitator, Mr. Nebbia leads focus groups and has facilitated codes/standards committee meetings. Research topics have included the valuation of energy-efficient innovation in homes, home fire sprinkler economics and impacts, disaster housing technical, economic, and social research needs, adoption of innovative technology in affordable housing, and the economic impact of energy-efficient retrofit/renovation programs on U.S. businesses.
As a technical consultant, Mr. Nebbia has supported the U.S. Department of Energy in various capacities over the past decade. Currently, he has the honor to serve as the Operations Director for the DOE Zero Energy Ready Home Program. He performed the same function for the predecessor program, the DOE Builders Challenge.
Mr. Nebbia holds a B.A. in Public Policy from Hamilton College.